Improved planning of manufacturing processes for individualized tools
Plamtex Int d. o. o. is a family-owned company with more than 25 years of experience in providing turnkey solutions as a one-stop shop. Company’s activities include technological development of products, development and manufacturing tools from testing prototype with injection moulding to manufacturing of plastic products in high-series. Manufacturing includes also tools for production of lighting parts for front and rear lights of premium vehicles of renowned automotive trademarks. To summarize, their manufacturing programme covers diverse plastic products for automotive industry, household appliances industry, optics, measuring instruments, etc.
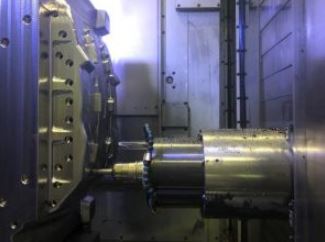
Production process phase
In collaboration with the researchers from Slovenia and Germany, the company has considerably decreased required time of tools manufacturing with the injection moulding for thermoplastics elements for automotive industry. As a result, the delivery of high-value added products increased and allows the company to sell more. In this research project were included researchers of the Computer Systems Department and the Department of Intelligent Systems at the Jožef Stefan Institute (Slovenia), while researchers from Germany came from the the Hahn-Schickard-Gesellschaft für angewandte Forschung e.V.
In the process of conceptualization of the solution proved as crucial expertise and knowledge on the fields of (1) the development of advanced computer structures and algorithms for processing big data, which represents one of the main research areas at the Computer Systems Department, and on the field of (2) research and development of intelligent systems, data mining and optimization, as research areas at the Department for Intelligent Systems.
Result
The developed technological solution lowers production costs with manufacturing tools for plastic products. Due to the fact, that the number of defects in tool manufacturing has decreased, the company achieved savings with materials and energy consumption, while at the same time the environment impact is also lowered.
Crucial step in the development of the solution was the use of artificial intelligence techniques (i.e. machine learning). With the great amount of data how the tools had been manufactured in the past, these techniques were used for predictive models of estimating duration of each step in the tool manufacturing process.
As a source for predictive models were used CAD plans for tools, information about the actual duration of manufacturing operations, available in the technology database, along with the expert knowledge about planning and manufacturing tools. Automatized prediction of operations duration supports company experts in the tool manufacturing optimizations, resulting in shortened manufacturing times, reduced waste, savings with the energy and option to prepare competitive business offers. Collaboration established on the technological challenge of the company resulted in a solution, that once again emphasized advantages of technology transfer from academic institutions to the industry.
Key success factors
Among key success factors of the research project were close collaboration and regular meetings between project group members, willingness of researchers to get acquainted with the basics of planning and of company experts to familiarize with the requirements for the use of new methods in the real environment, along with the data availability in expert knowledge, required for the project phase of machine learning. Another important factor was the role of the Center for the Technology Transfer and Innovation at the Jožef Stefan Institute, that cooperated with project members from the beginning, when it was essential to find relevant partners in each of technology centers, later participating in the project, until the later stages of the project when the company improved manufacturing process with the developed technology.
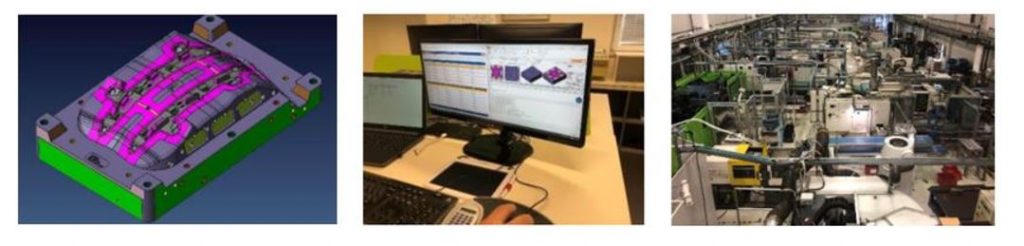
Overview of manufacturing processes with the support of predictive models (co-developed by the researchers at the Jožef Stefan Institute)
Cooperation took place under the frame of the project KET4CleanProduction, where additional presentation of this succes story is available.
The research project was formed and financed with the support of the Center for Technology Transfer and Innovation at the Jožef Stefan Institute.