MAHLE Electric Drives Slovenija d.o.o., with headquarters and manufacturing facilities in Šempeter pri Gorici, is part of the global group MAHLE GmbH from Stuttgart and is an internationally established manufacturer of starters and alternators for internal combustion engines, autonomously powered direct current electric motor systems and other advanced components for the automotive industry.
In their product development, the company utilizes state-of-the-art approaches and cooperates with research institutions. This is also true in the design of a synchronous electric motor with surface-mounted magnets, which is a part of the automotive steering system. The project objective was the technical and economic optimization of the electric motor, i.e., the determination of its geometry and the material properties of its components in such a way that the motor meets all technical requirements and its price is minimal.
The company started looking for a solution in cooperation with researchers from the Intelligent Systems Department and the Computer System Department of the Jožef Stefan Institute. The company and the researchers were assisted by the Office for Substantive Project Support, Technology Transfer and Innovation and the Office for Industrial Liaison at the Jožef Stefan Institute. They initially identified the key technological and development challenges faced by the company. They then established contact with the two research departments, recognizing their knowledge and expertise in developing customized technological solutions. Additionally, they supported the researchers while preparing potential approaches and methods to address the challenge, moderated the negotiations, and formalized the agreement on cooperation and intellectual property rights.
During the collaboration, an iterative computer-aided optimization procedure was developed, coupled with a numerical simulator of candidate solutions based on the finite element method. Here, the key issue was the high computational complexity of individual simulations and, as a consequence, of the entire optimization procedure. To speed up the calculation, the procedure was enhanced in several ways: efficient surrogate models were included, it was run in parallel on multiple cores, and the solution evaluation was carried out in several steps, making it possible to eliminate specific infeasible solutions without computationally demanding simulations. The next concern was the necessity to ensure the robustness of solutions, considering tolerance deviations in the manufacture of electric motors. This was ensured by evaluating feasible motor designs on a sample of implementations with various deviations. Finally, in addition to producing numerical results, the procedure was also required to provide insight into the solution space and to help the designers better understand the problem. For this purpose, the methods for data analysis and visualization were incorporated into the optimization environment.
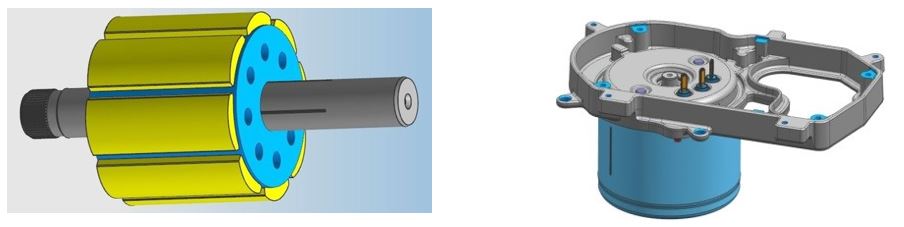
Electric motor of the automotive steering system
Key to the development of the solution were the skills of the participating researchers in utilizing metaheuristic optimization with surrogate models, high-performance computing, and data analysis and visualization. The project team from the company contributed their knowledge on electric motors and their design, the initial solutions for the optimization process, and the software and licenses required for electromagnetic modeling using the finite element method.
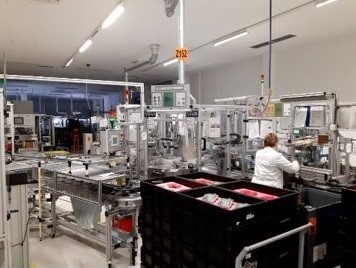
Production of electric motors for automotive steering systems
The result of the collaboration is the design of the active parts of the electric motor, determined by the values of its dimensional and material parameters. The obtained values of these parameters ensure rational use of components, the maximum possible fulfillment of customer requirements concerning the electric motor characteristics, and its cost efficiency. The cost of the components for the optimized motor design is 10% lower than for its initial version. Considering the fact that several million pieces are manufactured during the entire production period, this represents substantial savings for the company and greatly improves their competitiveness in the market.
For this achievement, MAHLE Electric Drives Slovenija d.o.o. and the Jožef Stefan Institute received the TARAS award at the IRT 2023 Industrial Forum in Portorož. The award recognizes successful cooperation between industry and research institutions in the fields of innovation, development and technology.
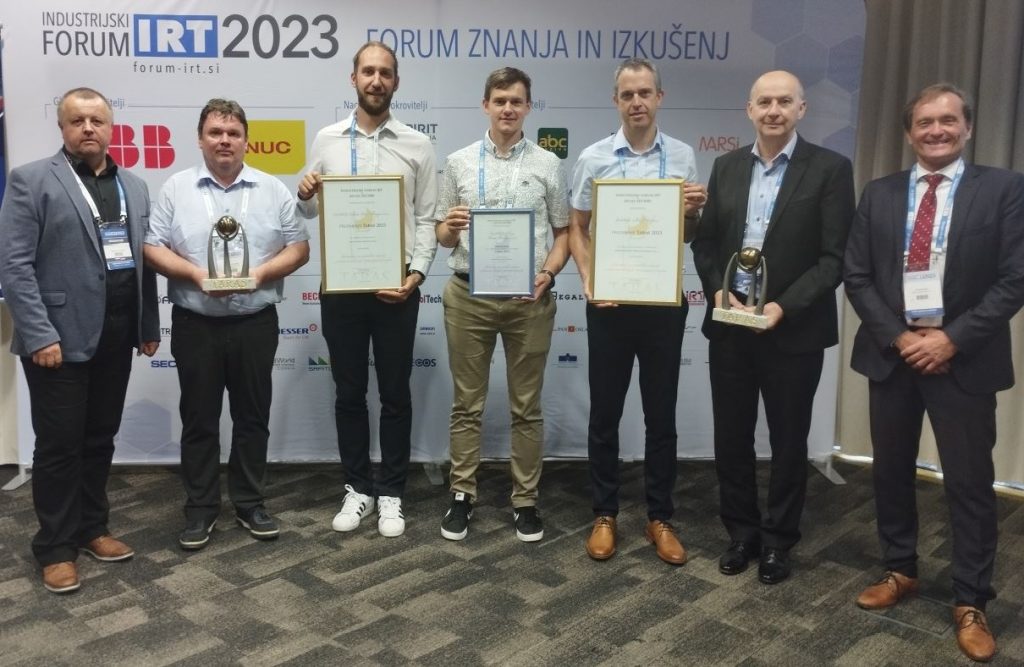
The TARAS award acceptance at the IRT 2023 Industrial Forum
The project was directly funded by the company MAHLE Electric Drives Slovenija d.o.o. The crucial contribution in establishing cooperation was provided by the Office for Substantive Project Support, Technology Transfer and Innovation and the Office for Industrial Liaison of the Jožef Stefan Institute.